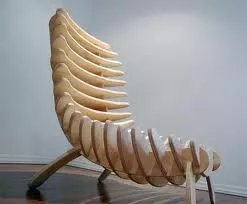
Что можно сделать из одного куска фанеры? Я долго думал и после некоторых поисков в сети наткнулся на интересное кресло в форме рыбьего скелета. "Смотрится отлично!", подумал я. Оригинальное кресло было разработано дизайнером Николосом Марзоунлиан и стоит аж 1100 фунтов (> 50.000 р ). Кресло продается, а значит чертежей к нему нет (хотя я не искал на sketchup warehouse), но конструкция довольно простая. Потратив некоторое время на осмотр фотографий, я принялся за работу. Кусок фанеры мне обошелся в 35 долларов (~1200р), работа - бесплатно, выгода делать самому очевидна!
Вы можете использовать любые инструменты и программы, которыми владеете, но так как я сам дизайнер/инженер и работаю с SolidWorks, я использовал именно ее. В ней удобно строить модели. VCarve Pro и Shopbot для ЧПУ. Если у вас нет всего этого, то вы можете использовать лобзик, потребуется чуть больше времени и усилий, но оно того стоит.
Скачать файл для программы ShopBot
Прикинуть размеры всех деталей на глаз по фотографиям было непросто. Сделав несколько набросков, покрутив их и повертев на бумаге и компьютере я примерно понял, что и где должно находиться, что к чему крепиться / прилегать и каких размеров это что-то должно быть.
Если вы заказываете часть материалов в интернет магазине, то не приступайте к работе, пока все они не окажутся у вас на пороге. Сосновая фанера, которую мне продали, должна была быть 1.78 см толщиной, но на деле оказалась 1.82 см. Пришлось делать поправки в ширине слотов на основной раме.
В 3D моделировании я новичок, так что этот этап у меня занял несколько часов. Нужно было смоделировать все компоненты, опять же их размеры, углы наклона и т.д. Детали, которые я в итоге смоделировал:
1. Спинка
2. Два ребра на 48 см (По сути дуги с небольшим радиусом кривизны и шириной 48 см)
3. Два ребра на 53 см.
4. 13 ребер на 58 см.
Плюсы программ моделирования в том, что можно "сложить" все куски вместе в самой программе, а значит не будет сюрпризов при состыковке готовых деталей.
Заготовки из SolidWorks я экспортировал в DXF и отправил в Vcarve Pro. Если у вас нет опыта работы с Vcarve то придется его наработать, хорошая новость в том, что это совсем не сложно. Хотя есть и другие программы для тех же целей, так что можете выбрать свою любимую/доступную.
Работая с Vcarve убедитесь что все вектора закрыты, все размеры/материалы корректны.
Я обещал рассказать про вариант, когда под рукой нет чпу. В этом случае его может заменить ажурная пила или лобзик.
Первое фото: это ребра в виде рогаликов. Если вы посмотрите на фото номер 4, то я пронумеровал там номер для каждого ребра. Так вот, ребра номер 18 и 1 - это рогалики с шириной 48 см. Ребра 2 и 17 - 53 см, ребра с 3 по 16 - 58 см. Все ребра схожи только в одном - расстояние между выемками 13 дюймов, или 33 см.
Второе фото: это ножки, расстояние между верхними выемками 13 дюймов (33 см), между самими ножками 45.5 см для передних, и 53 для задних. Ширина ножек 7 см.
Третье фото: это спинка. Сидушка 50 см в глубину, спинка 76 см в высоту, сами ребра 10 см в ширину.
Безусловно, перед началом такого проекта вам понадобится немного навыков, опыта и терпения, особенно если вы будете работать лобзиком, а не на станке. Распиливать все детали придется с высокой точностью. Но оно того стоит, и кстати сидеть в таком кресле намного удобнее, чем кажется.
Успехов!